Results for Brown Board Machines
The higher machine speeds and greater use of recycled fiber make machine runnability of Brown Board grades more of a housekeeping issue (trim squirt splatter) that can limit steam application on the Fourdrinier.
With lighter grades and accompanying much higher press loads, it is more efficient to locate the steam showers in the press section than on the Fourdrinier. Optimum location on a Linerboard machine is in a double-felted suction press nip. Bi-Nip and Tri-Nip tunnels are an especially good location.
Many Brown board grades utilize a high impulse Shoe Press. Hot Pressing with steam is particularly advantageous for Shoe Pressing.
Any machine making 100% recycled fibers or a grade that contains waxes should consider a Lazy Steam Injector over the Uhle box to help uniformly condition the press fabric. Steam application is an affordable and environmentally safer means to condition press fabrics and also allows more latitude in their design.
Any profiler should be used to improve moisture uniformity. To increase dryer-limited production or reduce dryer steam demand, a Lazy Steam Injector should be used in suction press nips to uniformly heat the sheet and enhance water removal.
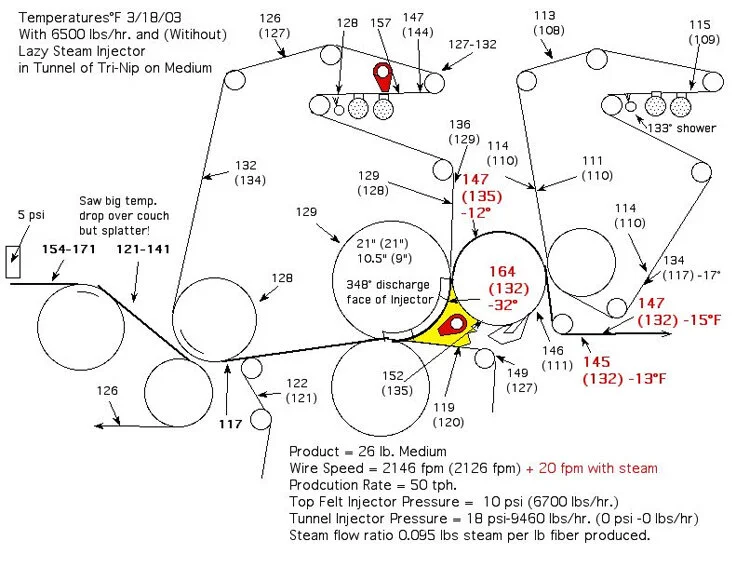
Example of temperatures with and without steam supply in "tunnel' of a Tri-Nip press on a Corrugating Medium machine. Machine speed immediately decreased 20 ft/min when the steam flow was shut off and average sheet temperature entering the dryer dropped 14 F. An injector over the Uhle box is also being used to heat the Pickup Felt on this machine. Red denotes "without" steam to tunnel injector.

Optimizing steam flow to Lazy Steam Injector in tunnel of a Bag Machine. By providing adequate injector steam flow, the entire tunnel was uniformly filled with transparent "lazy" steam to both high-vacuum suction nips. Red denotes "lazy" steam coverage with the slightly higher flow needed for this particular application that resulted in a significant sheet temperature increase (9 F).
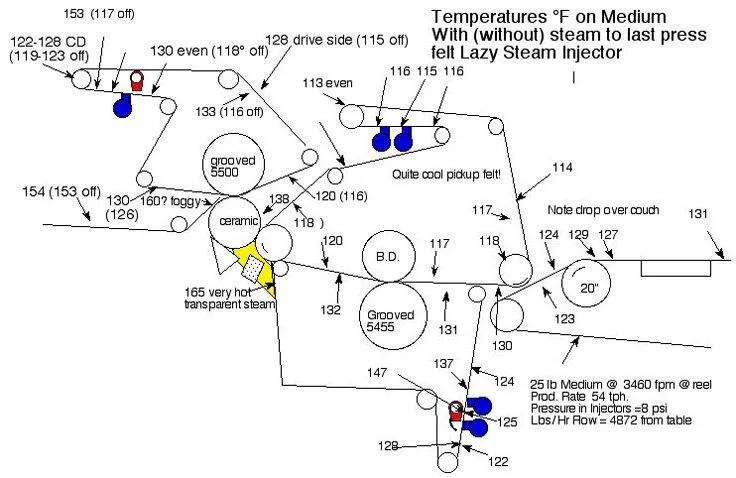
Lazy Team Injectors on Bottom and 3rd Press Top felts on a Corrugating Medium machine. The modest increase in felt temperature dramatically reduced the amount of wax in the fabrics, resulting in much improved machine runnability. A 3rd Lazy Steam Injector was soon added to the Pickup Felt and this reduced the number of breaks at the Pickup position from 26 per month to virtually zero.